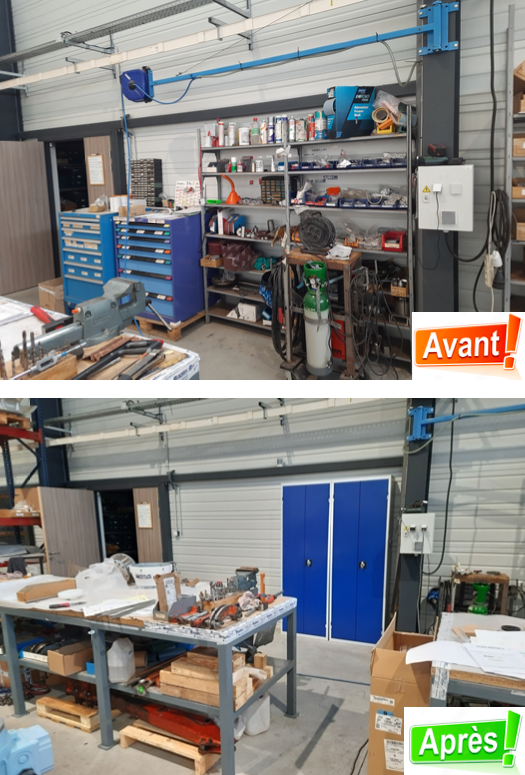
News
MAXIMISING ORGANISATIONAL EFFICIENCY : implementing the 5S method
In an increasingly competitive business landscape with ever-growing customer demands, every advantage in efficiency and productivity counts. One of the most effective approaches AGITEC has found to achieve these goals is the 5S method. This visual management and organisational practice has its origins in the principles of lean manufacturing (an optimisation method aimed at reducing the time needed for production).
Popularised by Toyota in the 1950s, the 5S method is now widely adopted in various industrial sectors. Its impact goes far beyond the simple organisation of workspaces; it encompasses a culture of continuous improvement and order, essential elements for the long-term success of any organisation.
WHAT IS THE 5S ORGANISATION ?
The 5S method is much more than just a system for organising the workspace; it's a visual management philosophy that aims to create an optimal working environment, conducive to productivity, safety and quality. The five 'S's are derived from the Japanese terms Seiri (Sort), Seiton (Tidy), Seiso (Clean), Seiketsy (Standardise) and Shitsuke (Follow). Each of these principles represents a key stage in the process of organising and maintaining efficiency in a professional environment. By combining organisational discipline with a people-centred approach, the 5S method fosters a culture of shared responsibility and continuous improvement within the various workspaces of a company.
IMPLEMENTING THE 5S ORGANISATION AT AGITEC
Interview with Samoa MILARET, QSE Manager
"Over the last few months, a significant increase in production had led to a surplus of equipment in the production workshop, even though major investments had been made three years previously to double the surface area. At the same time, some employees were expressing a desire to review their working methods in order to increase productivity and efficiency. Faced with these challenges, we had to find a way of optimising workspaces while at the same time enhancing safety within our workshop for the production of made-to-measure industrial mixers. So we decided to implement the 5S method, an approach already approved by other manufacturers.
To facilitate this organisational transition, AGITEC benefited from CETIM's Ambition programme, supported by the Auvergne Rhône-Alpes Region. After an in-depth diagnosis of the company, the definition of objectives and the development of an action plan, we have all the tools we need to apply the 5S method within AGITEC.
THE IMPLEMENTATION
Having decided that the 'assembly' area of our production workshop would be the first to benefit from this approach, we set up a working group bringing together the people involved: the workshop manager, the assembly technicians and the warehouse receptionist. This area, which requires a major overhaul to increase its efficiency, is also important as a showcase for the company during customer visits, for example.
The first phase consisted of sorting the equipment and tools shared by all the employees, keeping only the essentials. Next, each employee sorted his or her own specific equipment, assigning it a colour code to symbolise its belonging.
The second phase involved a complete clean-up of the area: floors, workbenches, shelves, everything was put under the microscope.
The third phase involved organising the space, assigning a specific place to each piece of equipment. Thanks to a colour code or markings on the floor, each item is now associated with a specific space in the work area.
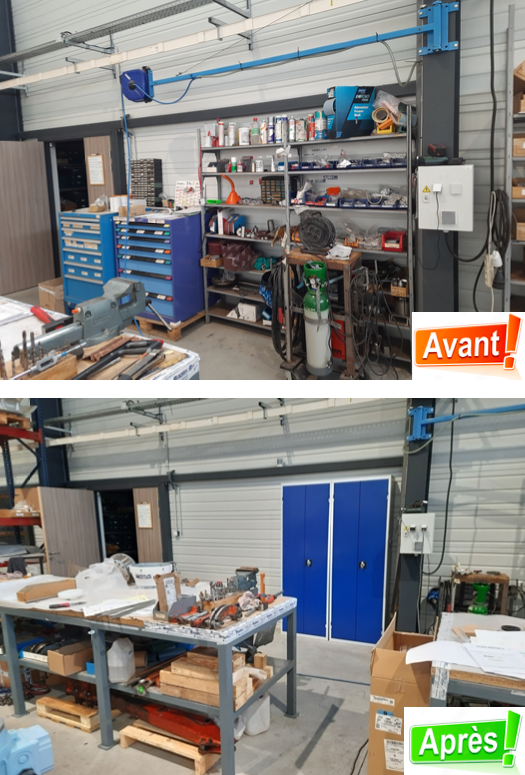
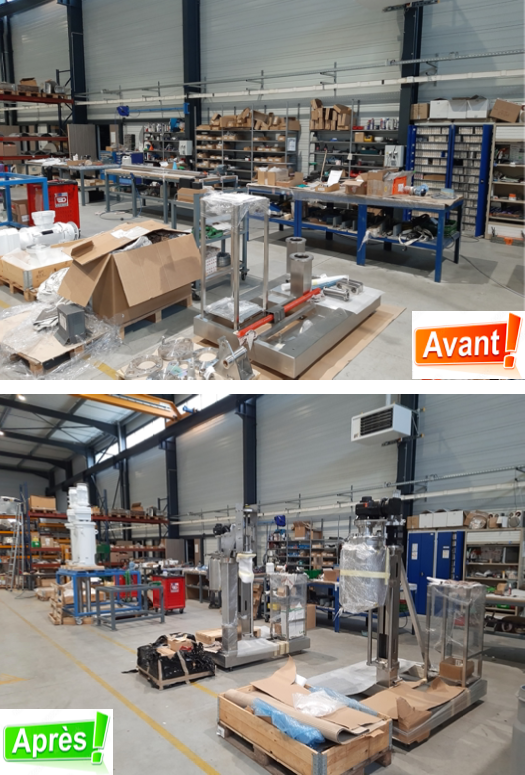
The fourth and final phase involved formalising the application of the method by establishing storage standards and cleaning rules. Visual documents, such as floor plans and photos of the premises, were placed in various locations to ensure continuity of the approach.
EMPLOYEE COMMITMENT
To maximise commitment, employees attended a meeting at which the method, its challenges and its benefits were presented. This initiative quickly met with a favourable response, as the employees themselves were keen to see improvements in the organisation of their workspaces.
THE RESULTS
The results were perceptible from the very first days: the "assembly" area was clearer and tidier, making for a more pleasant working environment on a daily basis. The employees enjoyed working in an environment that was conducive to carrying out their tasks.
In the future, the company plans to extend this method to other areas of the workshop, and even to the offices, particularly for administrative tidying."
In conclusion, the implementation of the 5S method has had a significant impact in optimising workspaces and improving operational efficiency within the company. Thanks to a methodical and collaborative approach, AGITEC has succeeded in transforming the production area, reducing clutter, introducing tidying and cleaning standards, and promoting a safe and productive working environment. With tangible results from the very first days, the company is now planning to extend the 5S method to other workspaces.